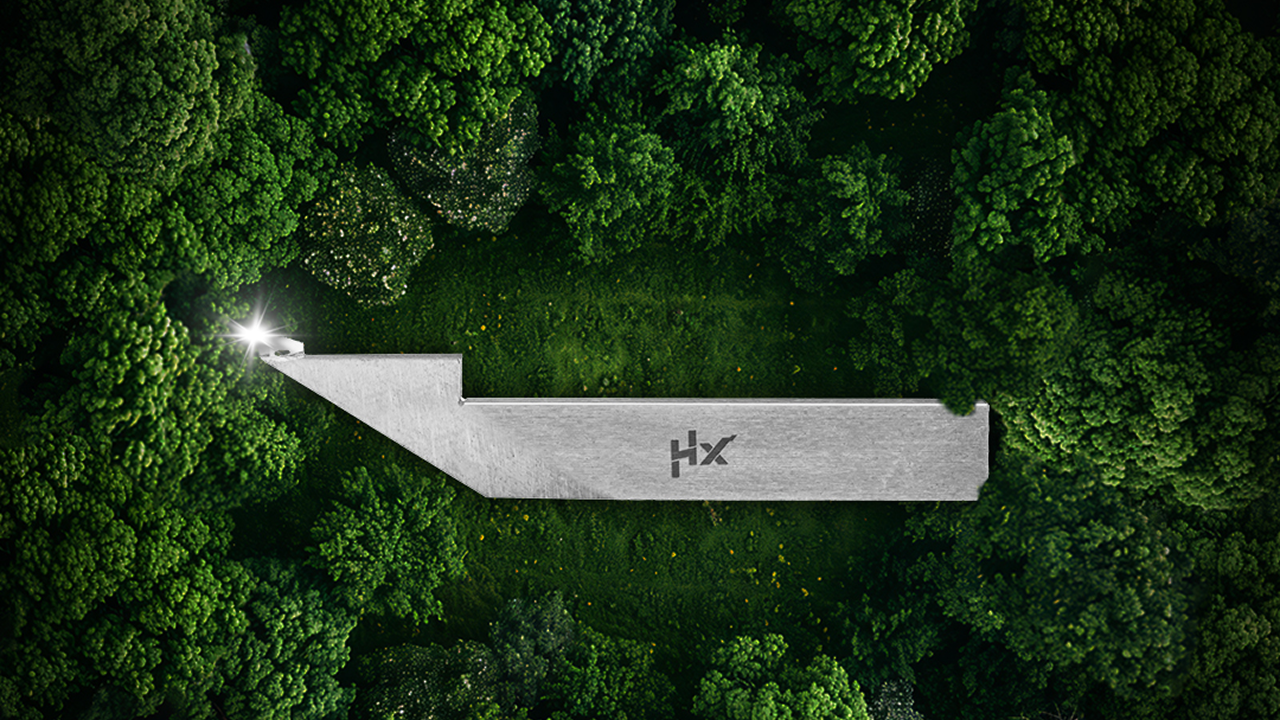
In today’s world, sustainability has become a necessity more than just a buzzword. Every industry is working towards reducing its environmental footprint, and manufacturing is no exception. Ultra-precision diamond (UPD) tools are proving to be a game-changer in the quest for sustainable manufacturing practices. These tools not only excel in delivering exceptional performance but also play a vital role in conserving resources and minimizing waste. Their durability ensures fewer replacements, reducing industrial waste, while their energy-efficient operations lower the overall carbon footprint. Additionally, the precision they provide minimizes material waste, making them an indispensable part of resource-efficient manufacturing. Here’s how:
Reducing Waste Through Longevity
One of the standout features of UPD tools is their unmatched sharpness and durability. Unlike conventional tools that wear out quickly and require frequent replacements, diamond tools maintain their precision over a longer period. This longevity means fewer tools are discarded, reducing the volume of industrial waste significantly. Along with this, the need for fewer replacements translates into a reduction in the energy and resources required for manufacturing, transportation, and disposal of new tools. By choosing UPD tools, industries can cut down their tooling expenses while simultaneously lowering their environmental footprint.
– Fact Check: The average lifespan of a diamond tool is up to 20 times longer than traditional carbide tools.
– Impact: Fewer tools manufactured and disposed of = lower resource consumption and reduced landfill waste. This leads to cost savings for manufacturers and a significant reduction in their carbon emissions.
Energy Efficiency in Precision Machining
Precision is key when it comes to reducing energy consumption, and UPD tools excel in this area. Their ability to achieve accurate results in fewer machining steps helps manufacturers lower energy usage during production. This not only accelerates the overall process but also ensures that resources like electricity and machine runtime are optimized. Furthermore, the reduced wear and tear on machinery caused by the superior performance of UPD tools leads to less maintenance, indirectly conserving energy and resources.
– Fact Check: because diamond is an excellent thermal conductor, these tools often operate at cooler temperatures, cutting down the need for additional cooling systems, which further saves energy.
– Impact: By minimizing energy-intensive steps and relying on diamond’s natural thermal conductivity, manufacturers save on both energy and operational costs.
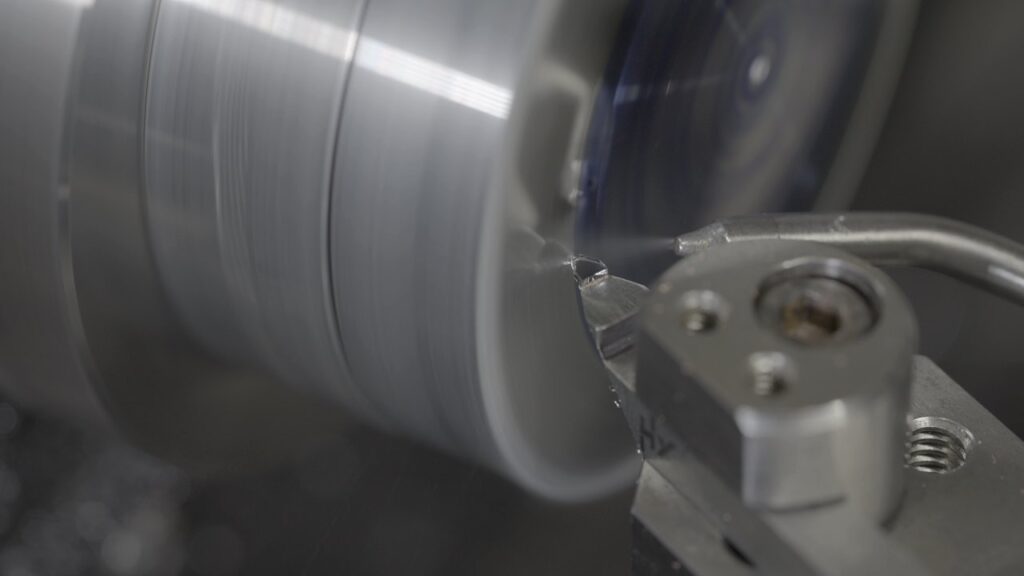
Minimizing Harmful Chemicals and Coolants
Traditional machining often relies heavily on chemical coolants to reduce heat and friction, which can have harmful environmental consequences. UPD tools, with their natural thermal conductivity and sharp cutting edges, require significantly less coolant or, in some cases, none at all. This reduces the environmental contamination caused by improper disposal of toxic chemicals while also cutting down operational costs for manufacturers.
– Impact: Lower dependency on potentially toxic chemicals not only improves workplace safety but also aligns with global efforts to adopt greener, more sustainable industrial practices.
Environmental Impact on Real-World Applications
Diamond tools are being increasingly adopted in industries where sustainability is a top priority.
Electronics Manufacturing:
These tools are used for machining components like smartphone lenses and silicon wafers, where their precision minimizes material wastage.
Aerospace:
In the aerospace sector, these tools help in machining lightweight materials like titanium and carbon composites, helping reduce aircraft weight and fuel consumption.
Automotive:
In electric vehicle (EV) manufacturing, diamond tools contribute to the production of energy-efficient components with minimal material wastage.
Supporting the Circular Economy
UPD tools contribute significantly to the circular economy by allowing refurbishment and recycling, ensuring minimal waste generation. Used diamond tools can be re-ground and refurbished multiple times to extend their lifespan, reducing the need for new raw materials and the environmental impact of manufacturing. This practice not only minimizes waste but also lowers carbon emissions associated with production. At Hardten we have initiatives for responsibly recycling worn-out tools ensure that materials are repurposed effectively, supporting sustainable manufacturing practices.
Innovations by Hardten in Promoting Sustainability
Sustainability happens to be a by-product of using Ultra Precision Diamond tools in the manufacturing industry, but at Hardten, it is a core principle engrained in everyone associated with the company. Some of the ways Hardten promotes sustainable practices include:
- Solar Panels at the Office: Hardten uses renewable energy to power its operations, reducing carbon emissions.
- Tree Plantation Drives: On June 5th every year, Hardten organizes tree plantation activities to contribute to reforestation and environmental conservation.
- Refurbishment Programs: Hardten actively encourages clients to participate in its tool refurbishment program, promoting a circular economy mindset.
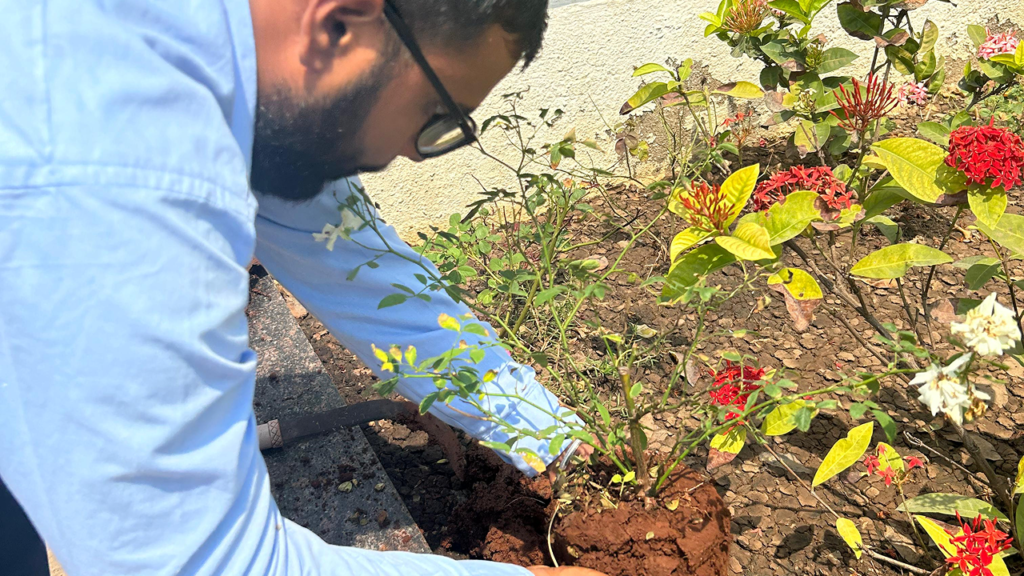
Conclusion: A Tool for the Future
Ultra-precision diamond tools go beyond their technical prowess—they’re a step toward a more sustainable future. By reducing waste, lowering energy consumption, and eliminating harmful chemicals, these tools are setting new benchmarks in eco-friendly manufacturing. Hardten takes pride in not just creating innovative tools but also in leading initiatives that align with environmental responsibility.
In an age where every step toward sustainability counts, UPD tools are not just a solution—they’re a necessity for industries looking to combine precision with purpose. Together, we can build a future where manufacturing leaves a lighter footprint on our planet.
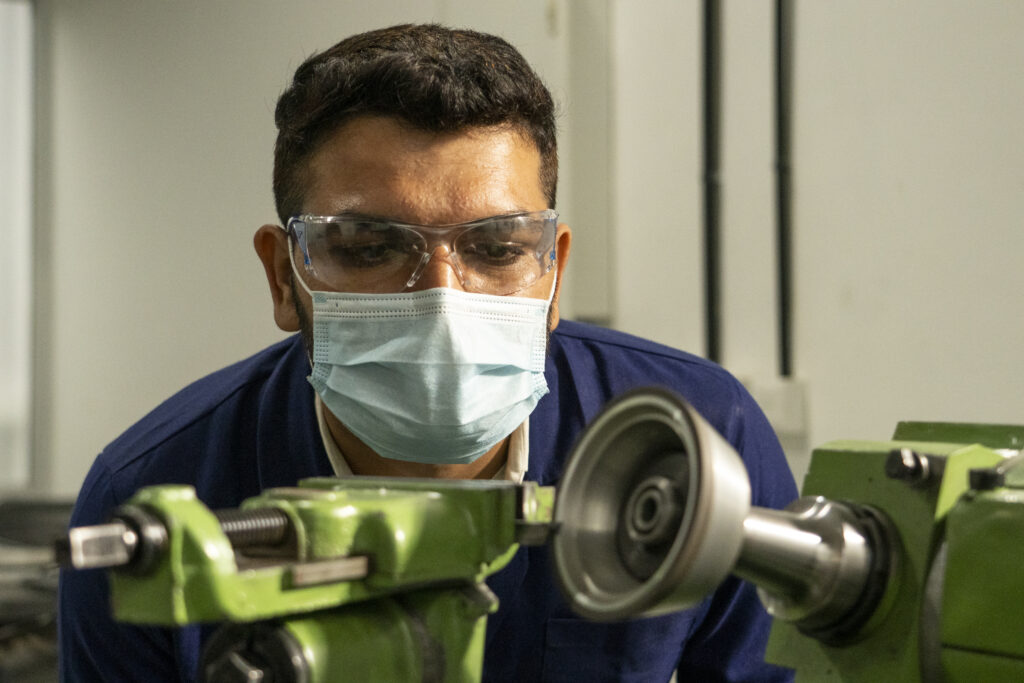